Heat Pipes
Heat pipes are used to transport heat over a distance with very low thermal resistance. This is very helpful when small or distant heat sources need to be dissipated over a larger area or moved to a remote heat exchanger. Heat pipes are a Fluid Phase Change application, often referred to as “re-circulating,” because they use a closed loop to transfer heat quickly through evaporation and condensation within the heat pipe.

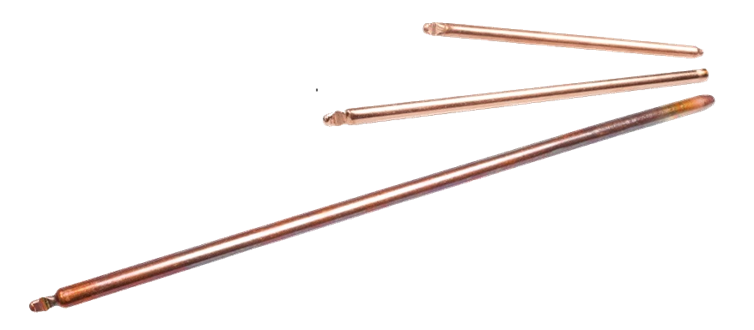
Heat pipes do not actually dissipate the heat to the environment, but serve to move heat efficiently within a thermal system. A heat pipe is a copper tube with an internal wick structure that is sealed on both ends with a small amount of fluid inside. The fluid, usually water, but can also be Methanol for working low ambient temperature application. As heat is applied to the pipe, the fluid will boil and turn to a gas, which then travels to the colder section of the heat pipe where it condenses back to a liquid. It is the evaporating and condensing of the fluid that form a pumping action to move the fluid (and thus the heat) from end to end of the pipe.
There are many types of wick structure that can be used within the heat pipe and they are generally classified into grooved, mesh, powder and hybrid. A grooved heat pipe is a copper tube with a series of shallow grooves around the internal perimeter of the heat pipe. While the fluid is a liquid, it travels in the grooves and while it is a vapor it travels in the open space of the pipe. Grooved pipes can be used in horizontal orientations, but are very limited in performance if used above 15° out of horizontal. A mesh heat pipe is a smooth wall copper tube with a woven copper mesh installed along the interior of the pipe. The mesh is designed to remain in contact with the walls of the pipe in areas where the pipe may be bent or flattened. Mesh pipes can be used in horizontal orientations up to 30° out of horizontal. A powder wick heat pipe can also be known as a sintered heat pipe.

Many thermal systems benefit from the addition of heat pipes, especially when heat sources are dense and/or remote to the final heat exchanger. Computer applications, such as processors, graphics cards and other chip-sets, have high thermally dissipated power in a small area. Fan heat sink combinations used in these applications can offer high-performance dissipation to the ambient, but much of the battle is to bring the heat to the heat exchanger with as little temperature change as possible. Heat pipes excel at this and can transport large heat loads from small areas with very little temperature difference.

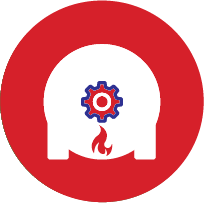
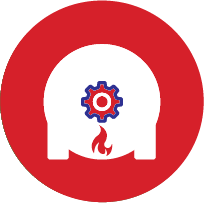
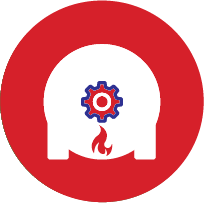
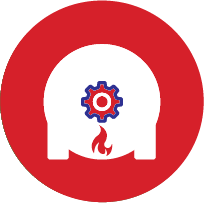
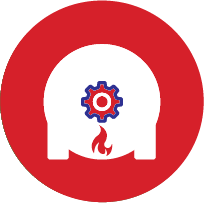
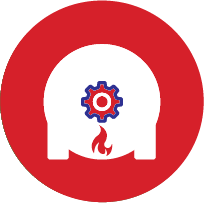